In other words, when the hydraulic pump is activated, it creates pressure in the fluid. It is then transmitted through the pipes or hoses to the cylinder, which converts the pressure into mechanical force. Moreover, the system’s pressure and flow rate can be regulated using various valves. This allows for more precise control over the operation of the equipment.
Hydraulic equipment employs the power of hydraulic fluid to generate force, movement, and control in a wide range of applications. This makes it vital for many industries, from manufacturing and construction to marine and aerospace. As a result, understanding hydraulic technology and its operation is essential for anyone working in these industries or interested in learning more about them.
With over 30 years of experience, Fluid Tech Hydraulics offers a diverse range of quality hydraulic and industrial equipment! Our commitment to innovation is evident in our continuous facility upgrades, state-of-the-art equipment, and expanded capabilities. Our goal is to ensure that our customers receive fast turnaround times while maintaining the highest quality of workmanship.
How Do Hydraulic Systems Work?
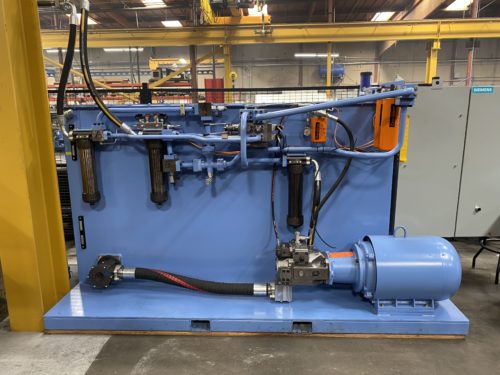
Types and Functioning of Hydraulic Equipment
Hydraulic equipment comes in various types, each with unique features and applications. The following are the different types often used in the construction, manufacturing, and transportation industries:
Hydraulic Pumps
Hydraulic pumps create a fluid flow in a system, which is then used to power hydraulic actuators like cylinders and motors. They work by creating a vacuum at the inlet side of the pump, which causes hydraulic fluid to be drawn into the pump. The pump then pressurizes the fluid and sends it to the outlet side of the pump, where it is then sent to the hydraulic actuators.
Hydraulic Cylinders
Hydraulic cylinders convert hydraulic power into linear mechanical force and motion. They are made up of a cylinder, piston, and hydraulic fluid. The pump pressurizes the fluid and sends it to the cylinder, where it pushes against the piston, causing it to move in a linear direction. They can also be single-acting or double-acting, depending on their utilization of the hydraulic pressure.
Hydraulic Motors
Hydraulic motors convert hydraulic pressure and flow into rotational mechanical power. They work on the same principle as hydraulic pumps, but in reverse — converting hydraulic power into mechanical energy instead of the other way around. They can also generate high torque at low speeds and are often more efficient than traditional electric motors.
Hydraulic Valves
Hydraulic valves control the flow and direction of the fluid in a system. They use a spool, poppet, or ball to regulate fluid flow through the valve body. An actuator — such as a solenoid or pilot valve — moves the spool, poppet, or ball. They are then controlled by an external device like a manual lever or a computer.
Hydraulic Hoses and Fittings
Hydraulic hoses and fittings transport fluid from one point in the system to another and connect different system components. The hoses are flexible tubes designed to withstand high pressures and temperatures and are often reinforced with steel or synthetic fibers for added strength. Meanwhile, the fittings connect the hoses to other system components, such as pumps, cylinders, and valves.
Hydraulic Power Units
Also called power packs, hydraulic power units are self-contained systems that generate power to operate various equipment. They draw fluid from the reservoir and send it through various components to generate the desired force or motion. These components include control valves, accumulators, and cylinders or motors.
Basic Hydraulic Equipment Design Principles
The principles behind hydraulic system design are rooted in the fundamental laws of physics and fluid mechanics. One crucial guide is using hydraulic fluid as a medium for transmitting force and energy. Hydraulic fluid is an efficient medium due to its nearly incompressible nature, which results in minimal energy loss. As a result, the systems are particularly useful in applications requiring significant force, such as those found in heavy machinery and construction equipment.Another crucial principle is the generation of movement through the application of pressure. In hydraulic systems, pressure is utilized to propel fluid through the system, which powers actuators like motors and cylinders. The regulation of fluid pressure permits precise control over actuators’ speed and force, enabling accurate movement control.
The final principle is managing fluid flow through valves and other elements. Valves are used to regulate the flow of fluid within the system, providing control over movement and force. Other components — such as reservoirs and filters — are also utilized to ensure the liquid remains impurities-free. This is particularly essential for sustaining the effectiveness and durability of the system.
Components of Standard Hydraulic Equipment
Standard equipment comprises several components that generate and transmit force using fluid. Each of the elements listed below plays a critical role in ensuring the system’s efficiency and reliability:
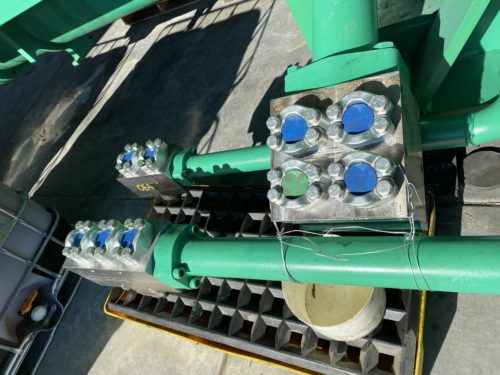
- Hydraulic fluid: This specialized liquid transmits the power in systems by facilitating force transfer from one component to another.
- Filters: These components remove contaminants and impurities from the hydraulic fluid to ensure its cleanliness and protect the equipment from damage.
- Accumulators: These store pressurized fluid, which can be released on demand to provide extra power, absorb shock, or maintain pressure in the system.
Pressure gauges: These instruments measure and display hydraulic fluid pressure, allowing operators to monitor the equipment’s performance and health. - Control valves: These regulate the flow and pressure of fluid within the system, providing operators with precise control over the speed and force of hydraulic actuators.
- Reservoirs: These containers store fluid and provide a means for replenishing those lost through leaks or system operation and dissipating heat generated by the equipment.
- Heat exchangers: These transfer heat the system generates to the surrounding environment. It results in the prevention of the fluid from overheating and causing damage to the equipment.
Advancements in Hydraulic Technology
In recent years, hydraulic technology innovations have greatly improved most systems’ efficiency and capabilities. Here are three of the most prominent technological advancements in this industry:
Electro-Hydraulic Systems
Electro-hydraulic systems integrate hydraulic components with electronic controls for better accuracy and efficiency. These controls regulate fluid flow, enabling electro-hydraulic systems to control actuators, resulting in smoother operation with higher precision. They can also decrease energy consumption and operating expenses by using only the required amount of fluid.
Hybrid Hydraulic Systems
Hydraulic technology has advanced with the development of hybrid systems that integrate pneumatic and electric components for enhanced efficiency and reduced emissions. They utilize electric motors to complement power, allowing for more efficient use of hydraulic power for each application. This decreases the size of the system, facilitating the development of powerful and more compact equipment.
Smart Sensors and Machine Learning Algorithms
Utilizing smart sensors and machine learning algorithms optimizes the performance of the systems. They allow data collection from various sensors and use algorithms to analyze the data and make real-time adjustments to improve efficiency and reduce energy consumption. They also enable predictions for potential equipment failures and schedule proactive maintenance to minimize downtime.